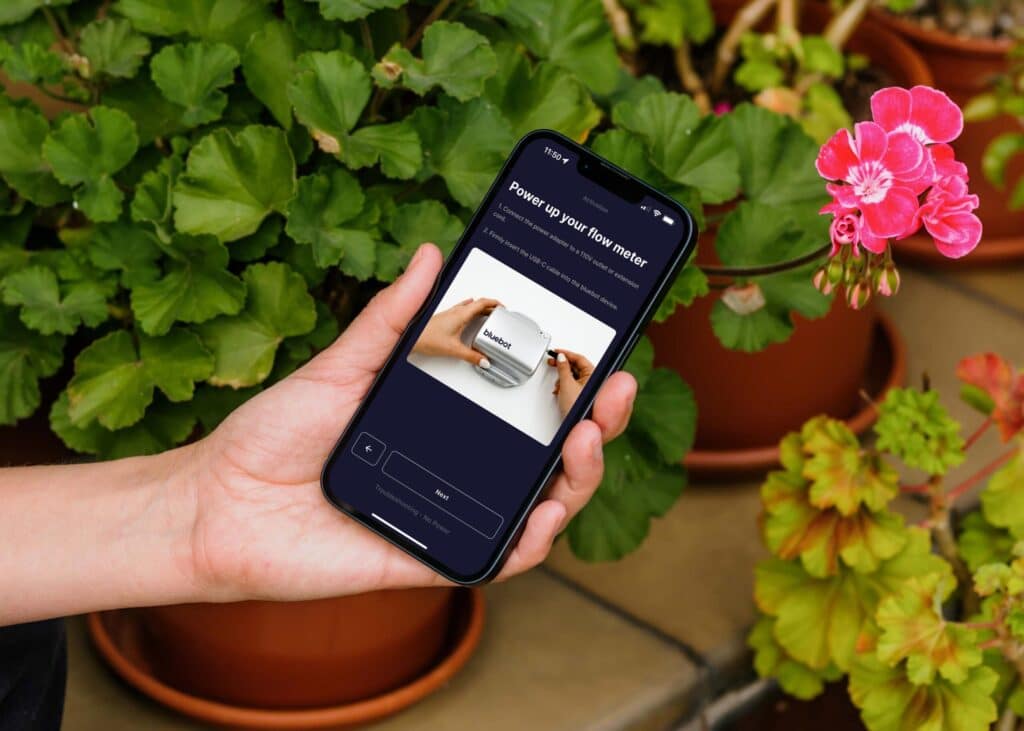
In today’s rapidly evolving industrial landscape, efficiency, accuracy, and reliability are paramount. Industries ranging from oil and gas to water treatment rely heavily on precise measurements to ensure smooth operations. One of the key tools that has gained popularity for flow measurement in these applications is the clamp-on flow meter. Unlike traditional flow meters that are installed within the pipeline, clamp-on flow meters are attached externally, making them a versatile and non-invasive option. This article explores the top benefits of using clamp-on flow meters in industrial applications.
1. Non-Invasive Installation
One of the most significant advantages of using a clamp-on flow meter is its non-invasive nature. Traditional flow meters require cutting into the pipe, which can lead to downtime and potential leaks. However, clamp-on flow meters are installed on the outside of the pipe, eliminating the need for any modifications to the existing system. This non-invasive installation not only reduces the risk of leaks but also preserves the integrity of the piping system. Additionally, because the installation process is straightforward and doesn’t require shutting down the system, industries can avoid costly downtime, which is particularly beneficial in continuous process environments.
2. Versatility in Application
Clamp-on flow meters are incredibly versatile and can be used in a wide range of industrial applications. They are suitable for measuring the flow of various liquids, including water, oil, chemicals, and even slurries. Moreover, these flow meters can be used on pipes made of different materials such as metal, plastic, and even concrete. This versatility makes clamp-on flow meters a preferred choice in industries with diverse flow measurement needs. Whether it’s for monitoring water usage in a treatment plant or measuring the flow of oil in a refinery, clamp-on flow meters offer a flexible solution.
3. Easy Installation and Maintenance
Installing a clamp on flow meter is a relatively simple process that does not require specialized skills or tools. The flow meter is attached to the outside of the pipe using clamps or straps, and the sensors are positioned to measure the flow accurately. Since there is no need to cut into the pipe or interrupt the flow, installation can be completed quickly, often in a matter of hours. Maintenance is also minimal because the flow meter does not come into contact with the fluid inside the pipe, reducing the risk of wear and tear. This ease of installation and low maintenance make clamp-on flow meters an attractive option for industries looking to minimize operational disruptions and reduce maintenance costs.
4. High Accuracy and Reliability
Accuracy is critical in industrial applications where precise flow measurements are essential for maintaining product quality and process efficiency. Clamp-on flow meters use advanced ultrasonic technology to measure flow with high accuracy. The sensors detect the time it takes for ultrasonic pulses to travel through the fluid in the pipe, allowing the flow meter to calculate the flow rate accurately. This technology is highly reliable and provides consistent measurements even in challenging conditions, such as when the fluid contains air bubbles or suspended solids. As a result, clamp-on flow meters are trusted for their accuracy and reliability in a wide range of industrial applications.
5. Cost-Effectiveness
The cost-effectiveness of clamp-on flow meters is another significant benefit. Because these flow meters do not require modifications to the pipeline, installation costs are lower compared to traditional in-line flow meters. Additionally, the lack of physical contact with the fluid reduces the need for regular maintenance and replacement, further lowering the total cost of ownership. For industries operating on tight budgets, the cost savings associated with clamp-on flow meters can be substantial. Moreover, the ability to install and maintain these meters without shutting down operations contributes to their cost-effectiveness by minimizing production losses.
6. No Pressure Drop
One of the challenges with traditional in-line flow meters is that they can cause a pressure drop in the pipeline, which can affect the flow rate and overall system performance. Clamp-on flow meters, however, do not come into contact with the fluid and therefore do not cause any pressure drop. This feature is particularly important in applications where maintaining a consistent flow rate is crucial. By eliminating the risk of pressure drop, clamp-on flow meters help ensure optimal system performance and prevent potential issues related to flow disruptions.
7. Suitable for Large Pipes
Measuring flow in large-diameter pipes can be challenging with traditional flow meters, which may require custom fittings and installation procedures. However, clamp-on flow meters are well-suited for large pipes because they can be easily attached to the outside of the pipe, regardless of its size. This capability makes clamp-on flow meters an ideal choice for industries such as water treatment, oil and gas, and chemical processing, where large-diameter pipes are commonly used. The ability to measure flow accurately in large pipes without the need for invasive procedures is a significant advantage in these applications.
8. Ideal for Hazardous Environments
In industries where safety is a top priority, such as oil and gas, chemical processing, and power generation, using a non-invasive flow meter is essential. Clamp-on flow meters are ideal for hazardous environments because they do not require any penetration of the pipe, which eliminates the risk of leaks or spills. Additionally, these flow meters can be used in areas where the fluid being measured is hazardous or corrosive, as the sensors do not come into direct contact with the fluid. This non-invasive design enhances safety and reduces the risk of accidents in hazardous industrial environments.
9. Data Logging and Remote Monitoring Capabilities
Modern clamp-on flow meters often come equipped with data logging and remote monitoring capabilities, allowing industries to track flow measurements in real-time and over extended periods. These features enable operators to monitor flow rates remotely, detect anomalies, and make data-driven decisions to optimize processes. The ability to log and analyze flow data is particularly valuable in applications where continuous monitoring is required, such as in water treatment plants, oil refineries, and chemical processing facilities. By providing real-time insights into flow conditions, clamp-on flow meters help industries improve efficiency, reduce waste, and ensure regulatory compliance.
10. Minimal Maintenance Requirements
Maintenance is a critical consideration in industrial operations, where equipment downtime can lead to significant production losses. Clamp-on flow meters require minimal maintenance because they are non-invasive and do not come into contact with the fluid inside the pipe. This design reduces the risk of wear and tear, corrosion, and fouling, which are common issues with traditional in-line flow meters. Additionally, because clamp-on flow meters are easy to install and remove, routine maintenance checks can be performed quickly and without disrupting operations. The low maintenance requirements of clamp-on flow meters contribute to their overall cost-effectiveness and reliability in industrial applications.
11. Portable and Flexible Usage
In some industrial applications, it may be necessary to measure flow at different locations within a facility. Clamp-on flow meters offer the flexibility to be easily moved and installed at various points along the pipeline. Their portability makes them ideal for temporary flow measurement needs, such as during system commissioning, troubleshooting, or maintenance activities. Industries that require occasional flow measurements can benefit from the convenience of a clamp-on flow meter, as it can be used across multiple sites without the need for permanent installation. This flexibility adds to the overall value of clamp-on flow meters in industrial applications.
12. Environmental Benefits
As industries become more environmentally conscious, the demand for sustainable and eco-friendly solutions is increasing. Clamp-on flow meters contribute to environmental sustainability in several ways. First, their non-invasive installation means that there is no risk of contaminating the fluid being measured, which is particularly important in applications involving drinking water or sensitive chemicals. Additionally, the lack of pressure drop and minimal maintenance requirements reduce energy consumption, contributing to lower carbon emissions. By choosing clamp-on flow meters, industries can enhance their environmental stewardship while maintaining efficient and accurate flow measurements.
13. Compatibility with Existing Systems
Integrating new equipment into an existing industrial system can be challenging, particularly if the equipment requires extensive modifications to the pipeline or control systems. However, clamp-on flow meters are designed to be compatible with a wide range of existing systems. They can be easily integrated into existing control and monitoring systems, allowing for seamless data collection and analysis. This compatibility simplifies the process of upgrading flow measurement capabilities without the need for extensive system overhauls. As a result, industries can enjoy the benefits of advanced flow measurement technology without the complexities of integrating new equipment.
14. Enhanced Process Control
Accurate flow measurement is essential for effective process control in industrial applications. Clamp-on flow meters provide reliable and precise flow data, enabling operators to make informed decisions and optimize process performance. By monitoring flow rates in real-time, industries can adjust process parameters to maintain optimal conditions, reduce waste, and improve product quality. The enhanced process control provided by clamp-on flow meters is particularly valuable in applications where tight control over flow rates is required, such as in chemical dosing, water treatment, and oil refining.
15. Scalability for Future Needs
As industries grow and evolve, their flow measurement needs may change. Clamp-on flow meters offer scalability, allowing industries to easily expand their flow measurement capabilities as needed. Whether it’s increasing the number of measurement points or upgrading to more advanced models with additional features, clamp-on flow meters can be easily adapted to meet changing requirements. This scalability ensures that industries can continue to rely on clamp-on flow meters as their operations expand and evolve, providing a future-proof solution for flow measurement.
Conclusion
The clamp-on flow meter has become an indispensable tool in a wide range of industrial applications due to its numerous advantages. From non-invasive installation and versatility to high accuracy and cost-effectiveness, clamp-on flow meters offer a reliable and efficient solution for flow measurement. Their suitability for large pipes, hazardous environments, and applications requiring minimal maintenance further enhances their value in industrial settings. With the added benefits of portability, environmental sustainability, and compatibility with existing systems, clamp-on flow meters are a smart choice for industries looking to optimize their operations and ensure accurate flow measurement. As technology continues to advance, clamp-on flow meters will likely play an even more significant role in helping industries achieve their operational goals.
- 0shares
- Facebook0
- Pinterest0
- Twitter0